Customer Profile:
Our client, a top-tier provider of fueling infrastructure solutions in North America, specializes in comprehensive turn-key services for distribution, construction, and maintenance. They are trusted for their strong partnerships with industry leaders and are committed to delivering reliable, high-quality fueling solutions.
Background:
To improve equipment management, the client needed a robust system to collect, analyze, and visualize data from multiple vendor sources. They aimed to enhance operational efficiency, reduce downtime, and enable proactive maintenance through real-time insights.
Client Requirements:
To address the complexity of managing diverse fuel-handling systems, our client outlined several important requirements:

Data Ingestion from Multiple Vendors
The solution needed to handle data from various fueling equipment vendors to ensure a unified data management approach across different systems.
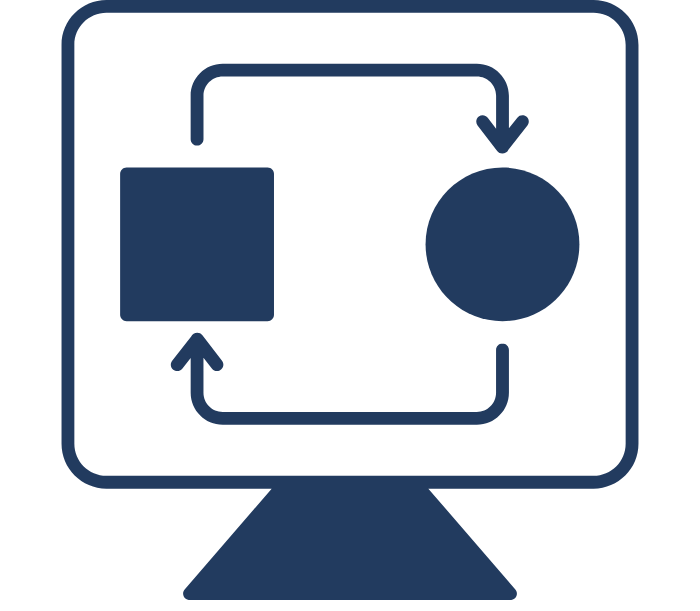
Data Transformation
Raw data had to be processed and converted into easily consumable metrics that provide clear operational insights.
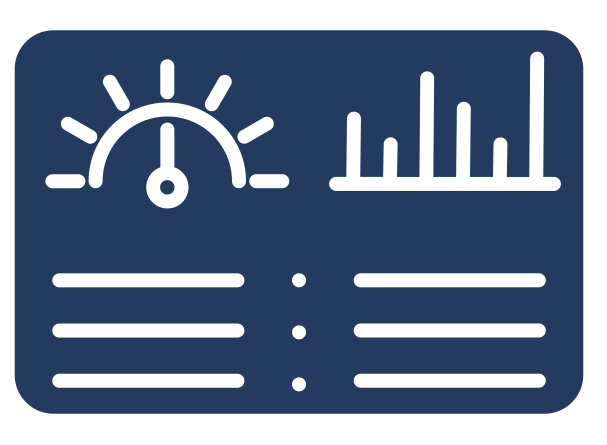
Visualization and Insights
The client required advanced visualization tools to transform this data into clear, actionable insights that would help guide decision-making processes.
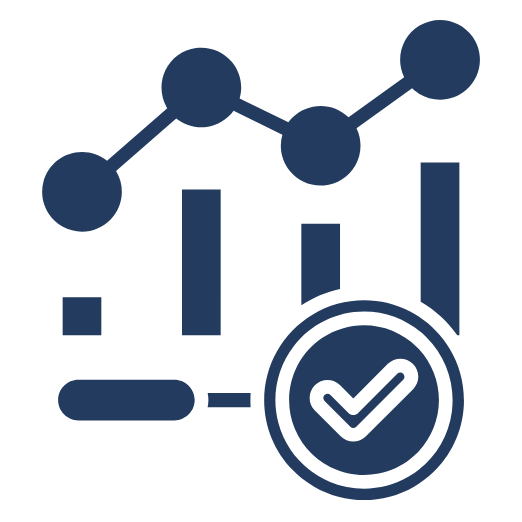
Predictive and Preventative Analytics
The solution had to offer intelligent diagnostics and maintenance capabilities to prevent equipment failures and reduce downtime.

Remote Troubleshooting
They needed the ability to troubleshoot remotely, reducing the need for on-site technician visits and minimizing operational disruptions.
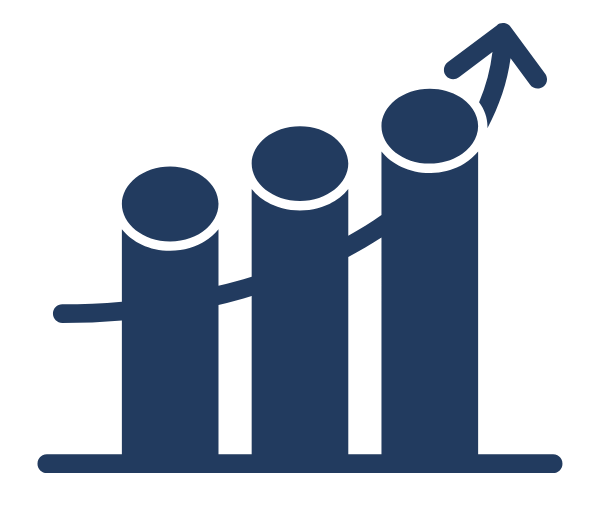
Scalability
As their operations spanned across multiple regions, the solution had to scale effectively, covering a wide geographical area while ensuring reliable local support.
Bridgera's Solution:
Bridgera customized and maintained the client’s platform, addressing their challenges through key technical features:
- Data Integration: Seamless data ingestion from multiple fueling equipment vendors provided a comprehensive view of the entire fueling infrastructure.
- Data Transformation: Raw data was converted into actionable metrics, simplifying fuel usage, equipment health, and operational insights for faster decision-making.
- Advanced Visualization: Using Kibana, data was presented through real-time dashboards, enabling quick identification of trends and issues.
- Predictive Analytics: Integrated predictive maintenance anticipated problems, reducing downtime and preventing equipment failures.
- Remote Troubleshooting: AI-enabled remote diagnostics resolved many issues without on-site technician visits, cutting costs and improving efficiency.
- Intelligent Dispatching: Automated diagnostics ensured technicians were dispatched only when necessary, minimizing unnecessary service calls.
- Scalable Architecture: The solution’s scalable design supported nationwide fueling systems while maintaining local service needs as operations expanded.
Results:
The implementation of Bridgera’s custom solution led to significant improvements in the client’s fuel and fluid management operations:
- Increased Efficiency, Reduced Downtime: Predictive analytics and remote troubleshooting minimized downtime, boosting operational efficiency and reducing disruptions.
- Better Data Access: Streamlined data from multiple vendors enabled faster, informed decisions, with advanced tools offering quick trend analysis and anomaly detection.
- Lower Costs: Automated dispatching and remote resolution cut on-site visits, reducing operational and maintenance expenses.
- Scalable Growth: The scalable system expanded with operations, ensuring national coverage and reliable local support.
- Proactive Maintenance: Predictive analytics enabled a shift to proactive maintenance, preventing costly equipment failures.
Conclusion:
Our client transformed their fueling equipment management with a powerful software solution that ingests, analyzes, and visualizes data from multiple sources, by partnering with Bridgera. The platform now enables predictive maintenance, remote troubleshooting, and advanced data insights, driving efficiency and reducing costs. Bridgera remains committed to helping organizations use IoT and data analytics to reform operations as the industry evolves.
Impact:
Bridgera’s solution had a transformative impact on the client’s operations. The platform reduced equipment downtime and enhanced operational efficiency by streamlining data from multiple vendors and enabling real-time insights. Predictive maintenance and remote troubleshooting lowered the need for on-site visits, cutting costs significantly. To sum up, our solution improved decision-making, optimized maintenance, and set a new standard for fuel management systems.